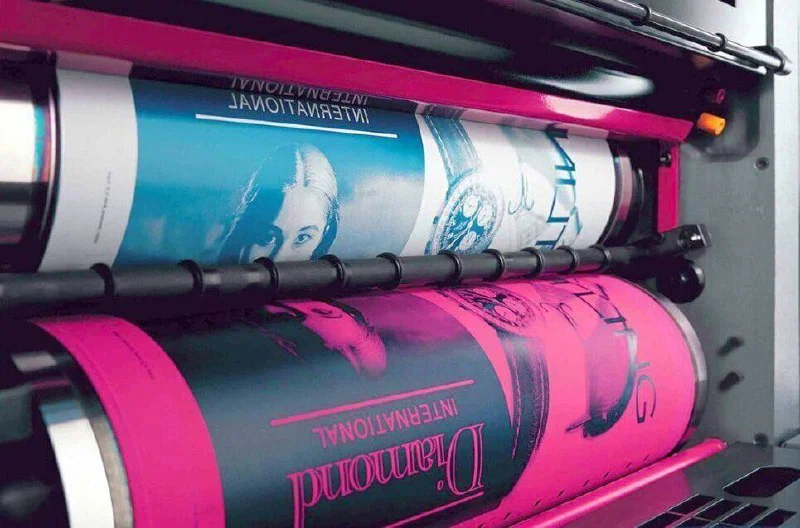
Offset printing is widely recognized as one of the most prevalent methods utilized today. With approximately 80% of printed materials produced using this technique, it has become a cornerstone of the industry. Offset printing involves an intermediary step between the substrate and the ink, setting it apart from previous methods. The introduction of offset printing machines in 1916 revolutionized the field by enabling the direct transfer of ink from the printing plate to the substrate through an intermediate cylinder, resulting in a non-mirrored image.
Details about the process
The offset printing process relies on planographic principles, where both printing and non-printing elements exist on the same level but differ in their physicochemical properties. An offset press, typically equipped with a plate cylinder and an offset cylinder, is used to execute the printing process. The plate cylinder holds the printing plate containing the desired elements. As the plate cylinder rotates, the image is transferred to the intermediate cylinder, which then imprints the image onto the substrate.
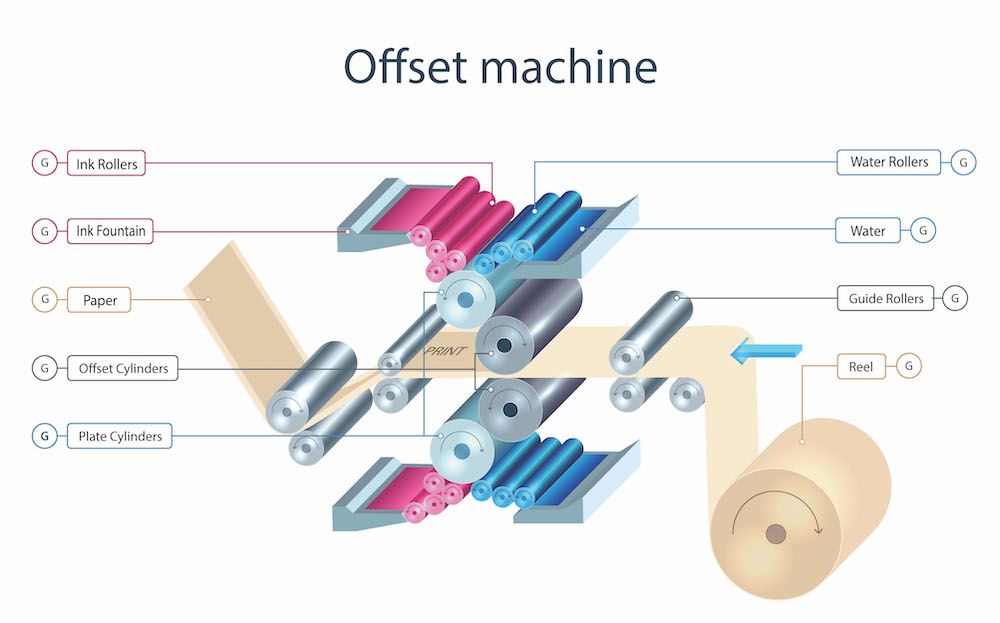
The inclusion of an intermediate cylinder plays a vital role in ensuring the even distribution of ink, leading to sharper and higher-quality printed images. Additionally, this design contributes to a reduction in equipment wear, enhancing the longevity of the printing machinery.
It is crucial to note that offset printing imposes strict and numerous requirements on artwork preparation, often necessitating the involvement of specialists to ensure optimal results.
Varieties
This type encompasses various methods and applications based on the ink application technique, equipment type, and printing formats. Understanding these variations is essential for determining the suitability of offset printing for different printing tasks. Let’s delve into the different varieties and their respective applications.
Based on the type of ink, it can be categorized as:
- Dampening (Wet) Offset. This traditional method employs liquid to repel ink, creating gaps between the printed marks. It is a widely used technique.
- Dry Offset. In this method, silicone is used instead of liquid to create gaps. While simpler, this technique requires ink with a special composition.
Based on the type of equipment, it can be:
- Sheet-fed Offset. This technology involves printing on individual sheets. Some sheet-fed machines may not be capable of printing full-color images in a single pass, necessitating multi-section machines for such requirements. Sheet-fed type is commonly used for business cards, brochures, flyers, labels, and booklets.
- Web (Roll) Offset. Prints are made on a continuous roll, which is later cut into individual sheets. Web offset machines offer high-quality prints with accurate color reproduction and vibrant colors. However, this technology requires expensive equipment typically found in large-scale print shops handling continuous high-volume orders.
Different machine models also offer varying printing formats:
- Narrow Format. This format involves a sheet width of no more than 60 cm. It is commonly used for printing business cards, brochures, flyers, labels, and booklets.
- Full Format. With a width of up to 102 cm, full-format models are suitable for producing books, catalogs, and periodicals. Some models even allow simultaneous loading of two rolls, enhancing efficiency.
- Wide Format. These machines can accommodate a canvas width of up to 190 cm, making them ideal for printing posters, maps, and billboards.
Which materials can be printed?
While this method is versatile, there are certain limitations and considerations for specific printing tasks:
- Printing white on colored paper may not yield desired results using offset equipment.
- Synthetic or metallized paper and film materials may not be suitable for offset printing.
- UV and foil inks are not commonly used in offset printing.
- Paper density requirements vary depending on the equipment type. Sheet-fed machines can handle denser paper, typically ranging from 80 to 420 gsm, while roll-fed machines are limited to a range of 35 to 150 gsm.
It is important to note that sheet-fed equipment is not commonly used for book and periodical production, as these applications require lighter-weight paper.
Understanding the varieties and applications of offset printing helps businesses make informed decisions regarding the most suitable printing method for their specific needs.
Pros and cons of offset printing
Advantages
Offset printing is a widely used technique in the printing industry, offering numerous advantages and a few limitations. While the specific circumstances and requirements of each printing task can influence the evaluation, we can highlight some general advantages and disadvantages of offset printing.
1. Economic Efficiency for Large Print Runs
Offset printing excels in terms of cost-effectiveness for large print quantities. As the print run increases, the per-unit cost decreases, making it an ideal choice for high-volume projects.
2. High-Quality Full-Color Printing
It delivers exceptional print quality with vibrant and accurate color reproduction. It allows for precise color matching, making it suitable for projects where color fidelity is critical.
3. Durability of Prints
Prints produced through this method exhibit excellent durability. They resist fading, making them suitable for long-lasting materials such as books, catalogs, and marketing collateral.
4. High Printing Speed
The presses are capable of high-speed production, enabling the printing of up to 10,000 impressions per hour. This efficiency is particularly beneficial for large-scale print runs with tight deadlines.
5. Additional Operations
Offset printing allows for the integration of various post-printing operations, such as folding, scoring, die-cutting, embossing, and lamination. This versatility enhances the aesthetic appeal and functionality of the printed materials.
6. Wide Range of Media Options
Offset printing supports a wide variety of media types, thicknesses, and formats. It can accommodate different paper stocks, including coated, uncoated, textured, and specialty papers, offering versatility in design and application.
Disadvantages
1. Lengthy and Complex Prepress Period
Offset printing involves a comprehensive prepress process, including layout preparation, intermediate forms, color proofs, and final print run setup. This intricate workflow adds time and complexity to the production timeline.
2. Economic Impracticality for Small Print Runs
It may not be cost-effective for small print quantities, typically below 400 copies. The fixed setup costs and longer setup time make it less efficient for short-run projects.
3. Limited Flexibility for Last-Minute Changes
Once the offset form is created, making quick modifications to the layout becomes challenging. The setup process and plate creation require time and investment, limiting the ability to incorporate immediate changes.
Understanding the advantages and disadvantages of offset printing helps businesses make informed decisions based on their specific requirements. By considering factors such as print quantity, budget, timeline, and desired print quality, businesses can determine whether this method aligns with their needs and goals.
How offset printing differs from digital printing?
Offset printing and digital printing are two prominent printing technologies used in the industry. While both offer high-quality results, there are notable differences in terms of the printing process, cost, speed, and printing possibilities. You can read how offset printing differs from digital printing in this article.
Determining whether offset or digital printing is better is not a straightforward answer, as it depends on various factors. The suitability of each printing process relies on specific printing tasks, print quantities, urgency of execution, and other relevant considerations. Evaluating these factors allows businesses to make informed decisions and choose the most suitable printing method for their unique requirements.